Tooling
The Class of a Production Mold is typically determined by the number of parts that will ultimately be produced by the tool. At Plastic Concepts & Design, Inc. we work with our customers to understand their long-term project goals in order to recommend and build a mold best suited to their particular application. For example, molds needed to produce a lower volume of parts can be made using softer steels (often P-20) saving our customers the expense of a tool made from hard steels or other costlier materials.
The Society of Plastics Industry Trade Association (SPI) categorizes plastic injection Production Molds into the following three classes:
Class 101 Injection Molds:
- Cycles: 1 Million or more
- Built for extremely high production, Class 101 molds require large capital investments and are manufactured with only the highest quality materials.
- Detailed mold design required.
- Mold base to have a minimum hardness of 280BHN.
- Molding surfaces (cavities and cores) must be hardened to a minimum of 48 R/C range. All other details should be hardened tool steels.
- Steels moving against one another should be dissimilar and have hardness differential of at least 4 Rockwell “C”.
- Ejection should be guided.
- Slides must have wear plates.
- Temperature control provisions should be in cavities, cores and slides wherever possible.
- It is recommended that plates and inserts containing cooling channels be of a corrosive resistant material or treated to prevent corrosion. Corrosion in the cooling channels decreases cooling efficiency thus degrading part quality and increasing cycle times.
Class 102 Injection Molds:
- Cycles: Not exceeding 1Million
- Built for medium to high production runs
- Good for abrasive materials and/or parts with limited budgets.
- Class 102 injection molds are fairly high quality, fairly high priced.
- Detailed mold design required.
- Mold base to be a minimum hardness of 280BHN.
- Molding surfaces (cavities and cores) must be hardened to a minimum of 48 R/C range. All other details should be made and heat treated.
- Temperature control provisions to be directly in the cavities, cores and slides wherever possible.
- Parting line blocks are recommended for all molds.
- Guided ejection, slide wear plastics, corrosive resistant temperature, control channels and plated cavities may or may not be required depending on the production quantities anticipated.
- It is recommended that a firm production quantity is determined for accurate quoting purposes.
Class 103 Injection Molds:
- Cycles: Under 500,000
- Built for low to medium production runs.
- Most cost-effective price range.
- Detailed mold design recommended.
- Mold base to be a minimum hardness of 165BHN.
- Cavity and cores must be 280BHN or higher.
- All other mold manufacturing specifications are optional
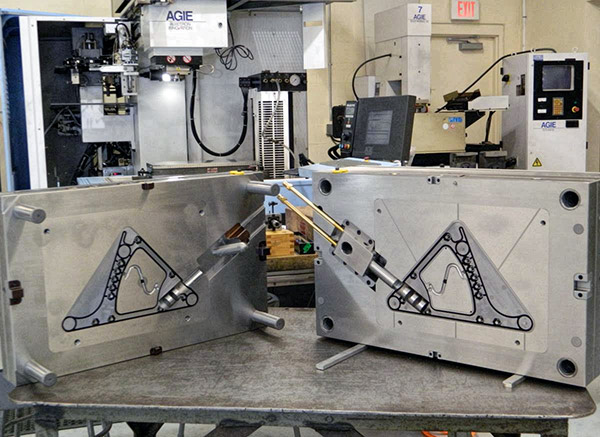